PRINCIPLES OF STORAGE AND TRANSPORT OF ABRASIVE TOOLS
Proper storage and transportation of abrasive tools Inspection of abrasive tools upon delivery
Storage and transportation of abrasive tools have direct impact on safety. Proper storage, transportation and awareness of existing hazards is crucial here. Grinding and cutting processes are characterized by very high dynamics; the peripheral speeds of 35 [m/s] often used, when converted, mean a speed of 126 [km/h], and 80 [m/s] is already 290 [km/h]. Therefore, the handling of abrasive tools requires special safety rules.
Proper handling at all stages of the logistics process, i.e. packaging, loading, protection against damage and weathering, external transport, handling at forwarding agents, unloading at the final customer, storage, internal transport, as well as during mounting and start up determines reliability of the tool and work safety.
Important transportation and storage issues (!)
- Abrasive tools, especially grinding wheels, although characterized by high resistance to a burst, are sensitive to impacts, drops, bending stresses and for these reasons require particularly careful handling.
- Impacts, throws or drops on a hard surface may develop scratches or invisible cracks, which can then lead to a bursting during operation and serious danger to life.
- It is unacceptable for abrasive tools to get wet during transport and storage, which can cause static imbalance, and in winter, cracking and destruction due to freezing water.
- Upon delivery of each batch of products, the condition of its packaging should be checked. If it is visibly damaged, an appropriate protocol should be drawn up together with the carrier, including identification data, a description of the damage and its consequences. In such a case the supplier should be notified as well.
- When receiving abrasive tools, it is necessary to carry out a detailed inspection for any damages and defects, preferably by sound test and visual inspection. Contact the manufacturer in case of any doubt.
- Unpacking activities should be carried out with great care. Clean tools with a brush or compressed air. Striking the wheels against each other is strictly prohibited!
- It is also the responsibility of the user / warehouseman to use protective pads (blotters) for safety clamping, if they are not glued but were delivered separately by individual arrangement. The pads should be transferred together with the grinding wheel to a mounting place or directly to the grinding machine.
- Particular attention should be paid to checking the operating speed of grinding machines so that the maximum permissible peripheral speed of the grinding wheel is not exceeded at a given station.
Methods for abrasive tool inspection upon delivery
Visual method and thus a careful inspection of the tool to detect any cavities, cracks or other signs of damage. Visible marks disqualify such grinding wheels - absolutely do not use. They should be set aside for re-examination by the manufacturer's service.
The sound (acoustic) method of testing grinding wheels involves tapping the wheels with a non-metallic tool, such as a wooden hammer. For heavier grinding wheels, set them on a hard clean floor surface. The best point to tap the grinding wheel is approximately 45˚ on either side of its vertical axis, near its periphery. Before each strike, turn it through 45˚ until it has been tapped around its entire circumference (see figure).

This method is primarily used for vitrified-bonded grinding wheels. A good grinding wheel produces a clear, resonant tone. A cracked grinding wheel produces a deafening tone that fades quickly. Such grinding wheels absolutely must not be used. They should be set aside for reexamination by the manufacturer's service. Resin bonded grinding wheels are tested in the same way, but in this case the tone is slightly less pronounced (muffled). The presence of a crack is also manifested by a change in tone.
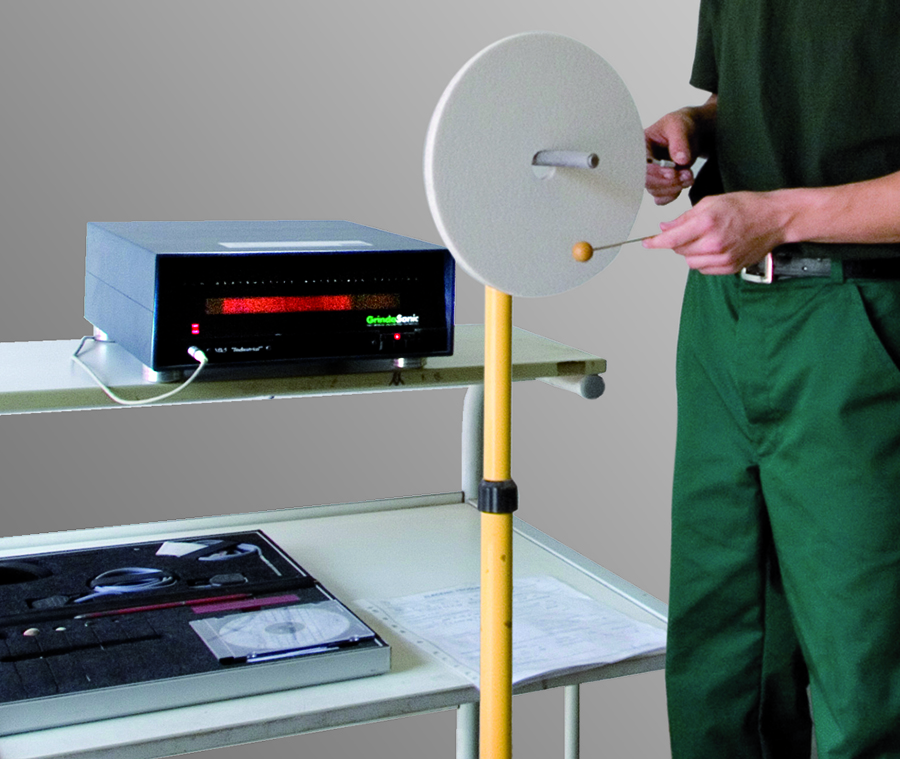
How to store abrasive tools
- For storage of abrasive tools, it is recommended to use dry, spacious, well-ventilated rooms with constant temperature, which should be about 10 to 30°C with humidity not exceeding 70%. In particular, the temperature in the room should not be lower than 4°C due to the possibility of damage to tools by water freezing in the pores. The last remark also applies to rooms where the grinding operation is carried out "wet", using coolant or there is a risk of moisture in the abrasive tool.
- Type B and BF resin bond abrasive tools are sensitive to moisture, alkaline and acidic environments and temperature changes. During storage, the bond can partially lose their properties and improper storage can accelerate this process. For this reason, they should not be stored in warehouses together with chemicals. It is important to avoid moisture as well as overheating, especially one-sided, by a close vicinity to heaters, for example.
- B and BF bonded grinding wheels for use on hand-held machines (with the exception of mounted points and wheels, plugs and cones) shall be marked with the expiration date. The date of expiry shall be within 3 years from the date of manufacture. It is expressed as month and year, for example. V04/2025.
- The way in which the grinding wheels should be laid is shown in the figure. The best and at the same time comfortable solution is vertical position of grinding wheels on two parallel wooden beams. Large grinding wheels are to be laid on beams placed directly on an even floor and other ones on suitably profiled racks with profiles and dimensions adapted to dimensions of wheels.
- Racks should be made of wood or steel lined with soft material, such as wood or rubber.
- The height of stacks of stored grinding wheels must not cause damage to them, especially those on the bottom of the stack.
- The same rules are to be observed when handling grinding wheels within the area of production shops as well as on working stands. Wheels are to be handled carefully to prevent dropping them or subjecting them to impact each other or hard objects.
- The position during transport should be similar to that on racks. Transport on trucks especially adapted for that purpose, padded with rubber and rubber wheels, is recommended. Wheels may be rolled along the floor provided that a suitable rubber blanket or other protection is available.
Example of a rack for storing grinding wheels
1 - small dish wheels
2 - small flat wheels
3 - shelves for small grinding wheels slightly inclined to prevent falling out
4 - back wall of the rack with protective lining
5 - flat grinding wheels
6 - small cylindrical grinding wheels
7 - large dish wheels
8 - taper cup wheels arranged edge to edge and bottom to bottom
9 - flat shelf for cuting-off wheels, shaped and cylindrical
10 - thin-walled or soft cylindrical grinding wheels
11 - corrugated separating cardboard
12 - steel or ceramic, even, flat supporting plate
13 - two-point cradle support for wheels standing on their circumference
14 - "front" of grinding wheel
15 - small cylindrical grinding wheels
16 - flat grinding wheels with a profile
17 - flat cutting-off wheels
18 - steel or ceramic, even supporting plate
19 - thick hard cylindrical grinding wheels
20 - medium-sized flat vitrified grinding wheels
21 - large grinding wheels
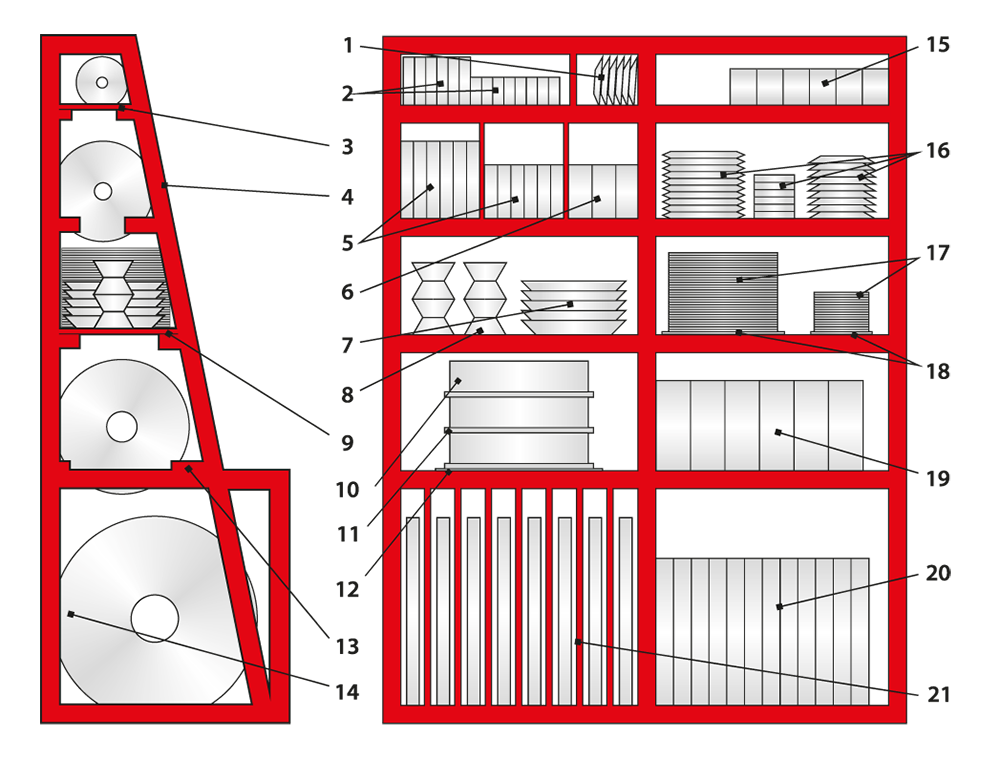
Since the beginning of its activity, ANDRE company has been focusing on high quality of its products. At ANDRE, every effort is made to ensure that products meet customers' individual needs and satisfy their highest expectations even in the most difficult grinding operations.
Abrasive tools by ANDRE ABRASIVE ARTICLES are safe.
ANDRE gradually improves its technological process to offer abrasive tools with increasingly better usability and a high safety factor in accordance with the applicable standards. Membership in organizations of leading abrasive tool manufacturers and regular certification fully confirm that.